
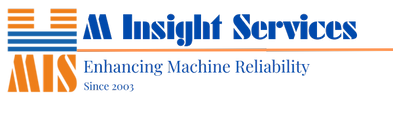.png)
FAQs
Have Questions? We Have Answers.
Explore our FAQ section to find detailed answers to common inquiries about our services, technologies, and practices. Our goal is to make your experience seamless and informative.
1. What is Vibration Monitoring & Analysis?
Vibration monitoring and analysis involve measuring and analyzing the vibration levels of machinery to detect imbalances, misalignments, and other issues that could lead to equipment failure. This helps in early detection and preventive maintenance.
​
2. How does laser alignment work?
Laser alignment uses laser technology to precisely align machinery components, such as shafts and pulleys, ensuring optimal performance and reducing wear and tear.
3. What is the importance of oil analysis?
Oil analysis helps in monitoring the condition of lubricants in machinery, detecting contamination, wear particles, and chemical composition changes, which can indicate potential issues and guide maintenance actions.
4. What are the benefits of thermography?
Thermography uses infrared imaging to detect heat patterns and anomalies in equipment. This non-invasive method helps identify overheating components, electrical faults, and other issues before they lead to failures.
​
5. What is in-situ balancing and why is it needed?
In-situ balancing involves correcting the balance of rotating equipment (such as blowers and rotors) while they are in their operational position. This method minimizes downtime and ensures that the equipment runs smoothly, reducing vibration and wear, and enhancing overall efficiency.
​
6. What are the advantages of using wireless vibration monitoring technology?
Wireless vibration monitoring allows for real-time data collection and analysis without the need for extensive wiring. Advantages include:
-
Remote monitoring capabilities
-
Reduced installation costs
-
Enhanced safety by minimizing the need for physical inspections
-
Immediate detection and reporting of anomalies
7. What are M Insight Services' operating hours?
Our company operates from Monday to Friday, from 9:00 AM to 6:00 PM. However, our maintenance workshop and support teams may be available outside of these hours for emergency maintenance requests.
8. How does M Insight Services ensure high-quality workmanship?
We ensure high-quality workmanship through a combination of experienced technicians, rigorous training programs, and adherence to industry best practices. Our team undergoes regular training and certification to stay updated on the latest techniques and technologies.
9. What safety protocols does M Insight Services follow during maintenance activities?
Safety is our top priority during maintenance activities. We strictly adhere to all relevant safety regulations and guidelines. This includes:
-
Conducting thorough risk assessments before starting work.
-
Providing personal protective equipment (PPE) to all technicians.
-
Implementing safety procedures and protocols to minimize risks and hazards.